Why Metallurgy Matters for Your Cutting Operation
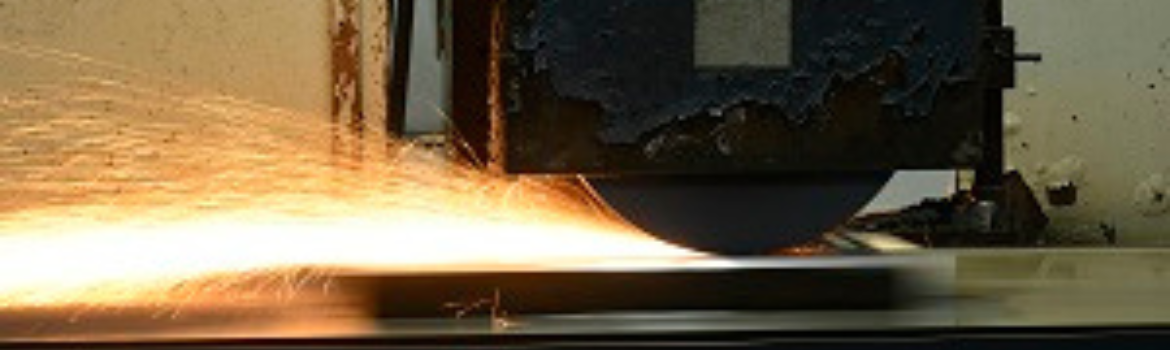
When it comes to manufacturing, distributing, and selling industrial knives and blades, metallurgy matters. A keen understanding of metallurgy plays a crucial role in determining what type of steel to use, when an element will enhance or detract from the performance of a cutting edge, and the overall durability of the end product. Metals are considered the backbone of the engineering industry. If your industrial knife supplier doesn't understand the behavior of the metals and alloys, they won't be able to effectively transform those raw materials into an end product that will provide a successful outcome for your cutting operation. Partnering with an industrial knife supplier with metallurgy knowledge and experience can make all the difference in your operation.
Iron is the base metal for steel and in its simplest form, steel is iron with carbon in it. Carbon is widely considered to be the most important form of commercial steel alloy because increasing carbon increases the hardness and strength and improves the ability to harden steel. Both a blessing and curse, the addition of carbon can also increase brittleness and reduces weld-ability. Carbon is present it all steels. More details about the composition of carbon steel can be found below.
The process of mixing a metal with a non-metal creates an alloy. When iron is combined with carbon, we call it carbon steel. But what about other alloys that can be created to make steel perform differently? There are many other elements that can be added to steel that make it perform differently. There is no right steel alloy. What you choose is entirely dependent upon your cutting application, your equipment, and your desired end results.
Metallurgy is a deep subject and the details are many. This article provides some basic information about the important steel alloys and some sample steels that contain those alloys:
Carbon
As noted above, carbon is present in all steels and is considered to be the most important hardening element. While carbon increases the strength of the steel, when added in isolation carbon can decrease toughness. ACE engineers like knife-grade steel to have >.5% carbon, which makes it "high-carbon" steel.
Chromium
Chromium can be added to steel for wear resistance, harden-ability, and most importantly, for corrosion resistance. A steel with at least 13% chromium is typically deemed "stainless" steel, though another definition says the steel must have at least 11.5% *free* chromium (as opposed to being tied up in carbides) to be considered "stainless". Despite the name, all steel can rust if not maintained properly. Adding chromium in high amounts decreases toughness. Chromium is a carbide-former, which is why it increases wear resistance.
Manganese
An important element, manganese aids the grain structure, and contributes to harden-ability, strength, and wear resistance. Manganese improves the steel (e.g., de-oxidizes) during the steel's manufacturing (hot working and rolling). This alloy is typically present in most food application steel except for A2, L-6, and CPM 420V.
Molybdenum
Molybdenum is another carbide former. It's known to prevent brittleness and maintain the steel's strength at high temperatures and is present in many steels and air-hardening steels (e.g., A2, D2). Our engineers always want to have 1% or more molybdenum because it is what gives steels such as A2 and D2 the ability to harden in air.
Nickel
The majority of stainless steel contains 8-10% nickel, which adds toughness. Nickel can be added to steel to increase strength and hardness without sacrificing toughness. At elevated temperatures, nickel can increase resistance to corrosion and scaling when introduced in the quantities in high-chromium (stainless) steels.
Phosphorus
We find that phosphorous is present in small amounts in most steels. Known for increasing strength and hardness, it also has a significant negative impact on toughness. In fact, phosphorous is often considered a contaminant.
Silicon
Silicon contributes to strength and hardness in steel. Like manganese, it makes the steel more sound while it's being manufactured. Soundness is the measurement of impurities such as sand inclusions, slag inclusions, macro porosity, and shrinkage in steel.
Sulfur
Typically regarded as an impurity, sulfur increases machineability but decreases toughness.
Tungsten
A carbide former, tungsten increases wear resistance. One of the oldest elements used for alloying steel, when combined properly with chromium or molybdenum, tungsten will make the steel what is considered a high-speed steel. High-speed steel is a subset of tool steels and is commonly used as a cutting tool material because of its ability to maintain its hardness. The high-speed steel, M2, has a high amount of tungsten. Tungsten is the strongest carbide former behind vanadium.
Vanadium
Another carbide former, vanadium contributes to wear resistance and harden-ability. Vanadium carbides are the hardest carbides. The addition of vanadium contributes to wear resistance. It also refines the grain of the steel, which contributes to toughness and allows the blade to take a very sharp edge. A number of steels have vanadium, but M2, Vascowear, PGK, and CPM T440V and 420V (in order of increasing amounts) have high amounts of vanadium.
American Cutting Edge offers a number of ACE brand replacement knives and blades in a wide variety of raw materials. Our customers rely on our ability to enhance OEM specifications to improve knives and blades by using different raw materials, coatings, or surface treatments to provide the end result needed. Working with an industrial knife and razor blade manufacturer and supplier who truly understand the effects of raw materials, alloys, and coatings can make an enormous different in the quality of your cutting operation, the life of your blades, and the performance of your equipment.
Contact the experts at American Cutting Edge to take advantage of their knowledge today!