Razor Blade Materials and Coatings
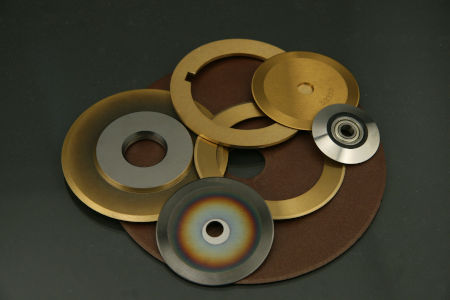
There are many considerations that go into determining the proper material and coating for your razor blade. The material being cut, the type of cut, the speed of the cut, and the desired durability of the blade all factor into selecting the proper material and coating. Below is a list of the most common razor blade materials and coatings American Cutting Edge offers. If you don’t see what you need or have additional questions then simply contact us, email us, or call us at 888-543-6860 and we can provide you proper guidance.
Carbon Steel:
- 1.2% High Carbon Steel: Premium grade of carbon steel for maximum sharpness and hardness.
- 1.1% High Carbon Steel: Premium grade of carbon steel for maximum sharpness and hardness.
- 1095 High Carbon Steel: Standard grade of carbon steel used on many common razor blades.
- 1075 Low Carbon Steel: Low grade of carbon steel or "blue tempered spring steel".
- Special alloy: Ask about our proprietary alloy that provides added strength and lifetime with maximum sharpness.
Stainless Steel
- 440 C Stainless Steel: Premium grade of steel for maximum sharpness and corrosion resistance.
- 440 A Stainless Steel: Premium grade of steel for maximum sharpness and corrosion resistance.
- 420 Stainless Steel: Standard grade of steel combining sharpness, corrosion resistance and cost.
- 301 Stainless Steel: Austenitic stainless steel for maximum corrosion resistance and strength.
High-Speed Steel
- M2 / M42 / Powered Metals: These materials offer maximum toughness and strength in high impact applications when blades break before they wear out.
Bi-Metal
- The strength and durability of a High-Speed Steel cutting edge combined with the low cost and ductility of a carbon steel base material.
Tungsten Carbide
- TWe have specialized grades of Ultra-Fine and Sub-Micron grain sizes that create pristine sharpness, high hardness, and strength. With 2 RMS surface finishing and each blade inspected at 50X, we provide a PERFECT blade, which lasts up to 100’s of times longer than steel blades, which are the best in the blade industry. Our re-sharpening program further increases the cost-effectiveness to the customer.
Zirconia Ceramics
- We use a unique grade of Zirconia ceramic. With similar properties to Tungsten Carbide, our ceramic material is even harder and more resistant to heat. This results in the longest-lasting blade in many applications. Our re-sharpening program further increases the cost-effectiveness to the customer.
Coatings: TiN / TiALN / TiC / Ceramic / Teflon™
- These are the most common coatings we offer for extended wear life on any blade. Ask us about these or describe your application. You can test options and select the coating that is best for you. We offer coatings that provide lubricity and strength that maximizes the blade lifetime and translates into production savings for our customers.
CONTACT US
Files and images associated with a quote request can be sent directly to: info@americancuttingedge.com