Preventive Maintenance for Your Pelletizer Blades
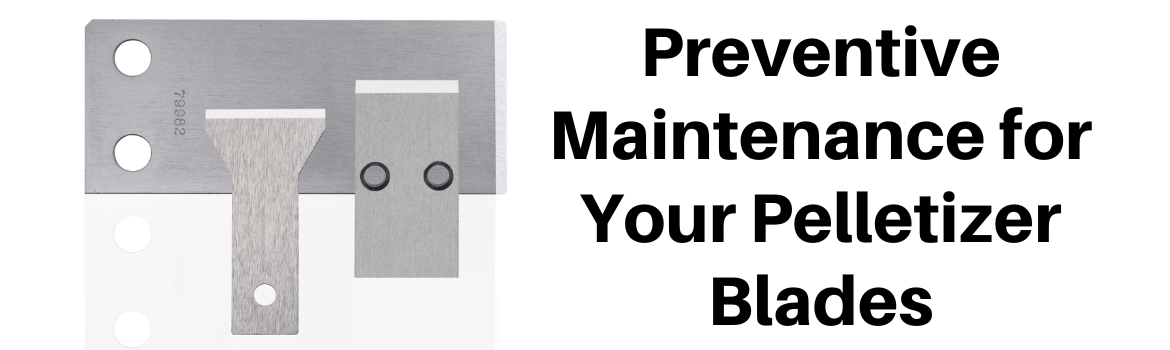
As a pelletizer, you understand the costs associated with downtime. You also understand the costs associated with procuring new blades and rotors. But did you know that you can control these costs with proper blade inspections and maintenance?
Continuous improvement is better than delayed perfection. “ Mark Twain
When the Unexpected Happens
While facilities that pelletize polypropylene materials, often run clean environments we understand that there are occasions when accidents do happen. Some of these customers run carbide inlaid pelletizer blades that are composed of a cold rolled steel, such as 17-4 or 440, and a solid carbide inlay that is brazed to the steel surface.
An ACE customer recently experienced the unexpected first-hand when a foreign object entered the pelletizer and reduced the carbide-inlaid mounted blade to bits. The foreign object hit the blade with such force that both the steel and the carbide portions of the knife shattered. However, what is significant to note is that the braze, connecting the carbide inlay to the steel, held together even under these extreme conditions.
In these configurations, the gap between the mounted blade on the rotor and the bed knife is as small as .002 to .004. This means that even the smallest piece of metal entering this area can cause failure of the bed knife or the mounted blade on the rotor.
In this case, to minimize downtime ACE sent a replacement knife out right away, and the machine was back up and running the next day. While this situation serves as an important example of maintaining proper policies and procedures, it also demonstrates the integrity of a well-made blade and the importance of performing consistent blade maintenance.
Prevention is better than cure. “ Desiderius Erasmus
Preventative Maintenance for Your Pelletizer
Too many pelletizing companies view preventative maintenance as optional. However, decreasing downtime and the overall costs of maintaining your machine depends on performing timely, preventive maintenance.
In pelletizing, each pellet must display consistent size and shape. When the size or the shape changes, facility managers and machine workers know there is a problem with the blades. However, when the pellets begin to display consistency issues, it is already too late to perform preventive maintenance. In an ideal scenario, blade maintenance is performed before pellet consistency is compromised.
Preventive maintenance of pelletizers requires looking for indications that the machine is working harder than it should to create consistent pellets. Some facilities find that running a tonnage metric is most effective. After the pelletizer has processed a specified weight of material, the machine, rotor, and blades are inspected for indications of wear and other maintenance needs.
The second approach to preventive maintenance is to monitor the RPM. If the equipment commonly runs at a consistent RPM with new blades installed, a spike in the RPM reading may indicate dull knives. Blades should also be inspected for chips, nicks, breaks, and proper seating each time the machine is brought down for scheduled maintenance.
However beautiful the strategy, you should occasionally look at the results. “ Winston Churchill
Maintaining Your Pelletizer Rotor
As one of the most critical parts of the pelletizer, the rotor blade must be consistently maintained to control costs and minimize downtime. Rotor blades that are not adequately maintained increase blade change-out frequency, which increases both downtime and the replacement blade costs.
Consistent, timely rotor blade sharpening allows facilities to get more life out of the blade. An ideal rotor blade sharpening schedule allows for minimal material removal to ensure a maximum number of sharpenings before replacement is necessary. However, when sharpenings are delayed, more of the blade material must be removed to achieve a sharpened edge, decreasing the overall life of the blade. Rotor blade sharpening costs a fraction of the price of rotor blade replacement. One to two extra sharpenings a year in lieu of a rotor blade replacement can quickly add up to significant savings.
Rotor blades sent to American Cutting Edge are inspected and analyzed to ensure compliance with the strict tolerances mandated by pelletizer OEMs. If sharpening is possible, the edge is perfected using a series of precision grinders. The rotor face is ground to remove imperfections and irregularities. Next, the gullet and flute are returned to their original geometry to ensure consistent pellet quality. Finally, we OD grind the rotor to guarantee concentricity with the outer diameter dimensions. This allows the rotor to be set at a .001 to .002 tolerance with the bed knife. If sharpening is not possible without compromising the integrity of the blade, the customer is notified.
Timely, proactive knife maintenance can dramatically improve the overall performance of your pelletizer and reduce the cost of blade maintenance and replacement. When these blades are well-maintained, you can expect to experience decreased downtime and improved production output.