Is Sharpening Your Pelletizer Rotor Worth the Cost?
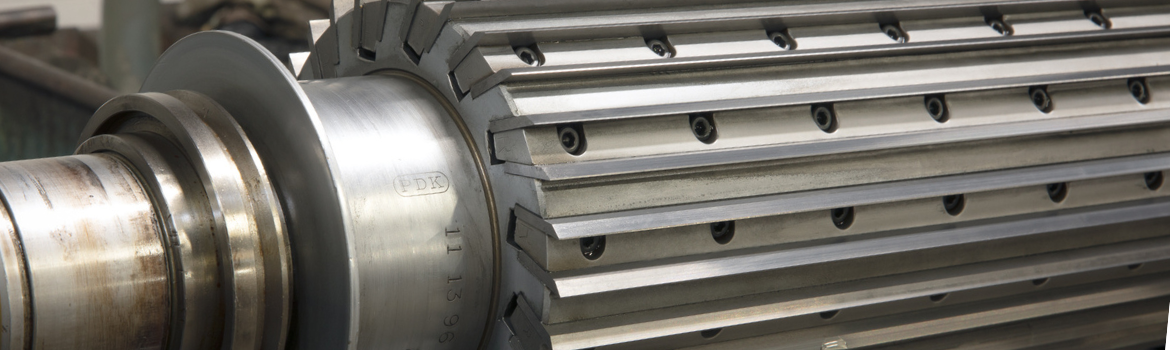
Industrial improvement projects often boil down to a central theme: do it better, for less cost. However, these two goals can seem run at odds with one another, but their opposition is only surface deep, especially where maintenance is concerned.
Most of us have experienced the frustration of a dead car battery or a flat tire. It always seems to happen at the most inconvenient time, causing us to miss out on an important meeting at work or a much anticipated social event.
In the moment, our actions are fueled by heightened anxiety. The issue must be resolved¦now! This urgent need drives us to spend more money on a fix than we would typically deem acceptable just to find a resolution as quickly as possible. If our tire blows-out on the highway or our battery dies in a dangerous part of town, our failure to perform preventive maintenance could even pose a physical threat, both to us and those around us. If we fail to get our oil changed on time, we are putting undue stress on our car's engine and are likely decreasing the useful life of the vehicle, which means that we will soon need to perform a more costly repair or even replace the car entirely.
Yet with all of this practical knowledge on the value of preventive maintenance, many industrial operations continue to forgo preventive maintenance in favor of reactive maintenance. Reactive maintenance saves money in the short-term, but those costs savings are quickly eaten-up and even exceeded down the road as more serious issues develop.
If you don't have time to do it right, you must have time to do it over. “ John Wooden
The Value of Opportunity Cost
For industrial pelletizers, rotors are one of the most critical replaceable components on the line. Pelletizer rotors are costly, and when one experiences a failure, the entire production line can come to a halt.
Unplanned downtime means that a failure occurs during what should be a productive time. When downtime arises unexpectedly, profits immediately start to feel the impact. Employees that are standing around, waiting for a repair are not producing, yet the labor dollars are continuing to add up. Customer delivery dates are not moving yet no product is coming off the line, meaning that expedited shipping fees may come into play.
Finally, in a rush to get production moving again, you may pay for rush delivery of a replacement or, worse yet, implement a quick-fix that only pushes the problem further down the line. All of this is incredibly frustrating, especially when you know that it could have been prevented.
You must have long-range goals to keep you from being frustrated by short-term failures. “ Charles C. Noble
Preventive Maintenance Saves Money
Preventive maintenance that is performed during scheduled machine downtime or when production is expected to be at its lowest minimizes the impact on the organization. Instead of maximizing exposure, businesses that plan for maintenance experience dramatically lower maintenance costs.
Waiting until pellets display inconsistencies, the machine fails, or for a rotor to break is reactive maintenance. It demands immediate action to return the line to normal production. However, catching a maintenance need before this moment saves time and money.
Adequate inspection and preventive maintenance programs prevent unnecessary downtime and the associated costs.
Treatment without prevention is simply unsustainable. “ Bill Gates
How to Perform Preventive Maintenance on Your Pelletizer Rotor
Prevent maintenance programs start with scheduled inspections. During scheduled downtime, inspect the rotor for evidence of chips, nicks, broken blades, or improper seating. If any evidence is found, immediately send the rotor for analysis and sharpening.
In addition to routine inspections, each pelletizing operation should include scheduled maintenance actions based on production. To determine the right maintenance interval for your process, work with an expert industrial knife manufacturer to adequately assess your rotor blades at various stages, including new, sharpened, and well-used.
Implementing a production-driven maintenance schedule ensures maximum rotor life and maximum production. When pelletizers elect to skip a sharpening in hopes of saving money, the result is often just the opposite. These rotors operate under a strict set of tolerances. When a blade becomes chipped or over-worn, more of the material must removed to return the rotor to the correct geometry. Removing additional blade material costs the rotor life and means that replacements will be necessary more often.
How is Rotor Maintenance Performed?
High-quality, precision rotor sharpenings require experience and expertise. Precision rotor sharpeners analyze each rotor blade, determine optimum rotor geometries, and return the rotor to like-new condition while removing the least amount of material. When sharpened by an industrial knife expert, the tolerances across your entire rotor are measured and maintained. Sending your rotors to an expert in pelletizer rotor blades provides the added benefit of in-depth analysis. Your industrial pelletizer rotor partner can alert you to potential operational issues that may be increasing maintenance costs or decreasing production volume or quality.
To ensure that your pelletizer rotors are always in peak condition, partner with an industrial knife expert that understands the importance of preventive maintenance and can help you determine an optimum preventive maintenance program.