How to Determine the Right Fit for Your Granulating Knife
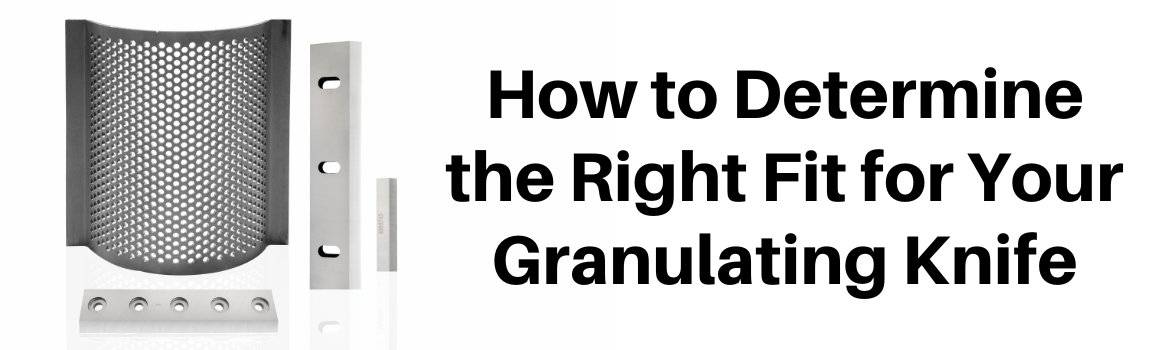
As a vital step in many production processes, granulating reduces materials, such as plastics, metals, and films so that it can be repurposed into other products. As the importance of reducing the amount of waste that enters landfills becomes more evident, granulating operations are increasing and facilities are looking for ways to improve efficiency and output.
Granulators with well-fit, sharp knives produce regrinds of a uniform size that are free from dust and fines while dull, ill-fitting blades do just the opposite, producing regrinds of various sizes that are peppered with dust and fines. Ill-fitting granulator blades also cause premature wearing of the knives and make it more difficult to accurately set the gap.
The gap between the rotor knife and the bed knife must be set based on the widest knife in the machine. When knives are not uniformly sized, gap increases cause inefficiencies. For example, in a granulator that contains three blades, two blades may be 3.005 inches and the third may be 3.010 inches. In a setup with a gap requirement of 0.005, two of the blades will actually have a gap of 0.010 while only one has a gap of 0.005. The material passes by two of the blades without being close enough to create a good pinch point. As a result, cuts are inconsistent, knives dull quickly, and the machine requires more amperage to complete the cuts.
Great things are done by a series of small things brought together.
“ Vincent Van Gogh
Granulating Blade Options
Many granulating machines allow for an array of choices for the rotor blade. This allows operators to determine the best cutting angle and material for their application. The best bevel design for the application is determined by the density, feed rate, and size of the machine in conjunction with the material to be processed.
Many recyclers utilize blades with a compound bevel or reverse bevel. This geometry provides added strength and is best suited to cutting dense materials and high volume granulating. A single keen edge design produces a cleaner cut but has a weaker cutting edge. This design is best suited to cutting film and other thin products in low volume processing.
Plastic molders often use a single bevel edge that is very sharp. This steep angled blade (often at a 70 degree angle) produces a shearing action. The hardness of the knife material can be reduced for running low volume batches to increase blades toughness and allow for the processing of a wide variety of materials and or shapes without damaging the cutting edge thus increasing blade life. Processing materials such as non-ferrous metal, requires a very blunt blade with a very tough edge.
Be a yardstick of quality. Some people aren't used to an environment where excellence is expected. - Steve Jobs
Finding the Perfect Fit
There are two ways to find the right fit for your granulating machine and process. The first is to begin with the make and model of your granulator and then select the bevel and material that best fits your operation. To gauge the effectiveness of the geometry and blade material, maintain a blade log that records cutting volume, knife condition, sharpenings, and blade life. Then, work with a custom blade manufacturer to optimize your knife to meet the needs of the business.
A second option is to reverse engineer a knife based on your current blade. When a high-quality industrial knife manufacturer is supplied with a brand new granulating knife, 100% of the specifications can be obtained. This allows the manufacturer to produce replacement knives that are identical or exceed the requirements of the current blades.
To reverse engineer a used granulating blade, high-quality industrial knife manufacturers perform metallurgy tests to reveal blade material and hardness. They also examine the wear pattern of the knife to check for damage to the cutting edge. Whether an industrial knife manufacturer is reverse engineering a new or used knife, a sample demonstrating the current wear pattern of the existing blades should be provided to enable analysis the cutting edge wear pattern.
Based on the information from these tests and analyses and the material being cut, engineers make recommendations to develop a knife design that improves performance. The result is increased production, improved knife life, and reduced dust and fines to ultimately produce more a consistent product.
If you define the problem correctly, you almost have the solution. “ Steve Jobs
Many knife suppliers take a one size fits all approach to granulating blades. However, the variations in machines, production volume, and material have a significant impact on the performance of granulator knives. To optimize your granulators production, work with a high-quality industrial knife manufacturer with the knowledge, experience, expertise, and capabilities to assess your granulating operation and recommend an ideal granulator blade.