The Best Blade Material for Your Shear Slitting Application
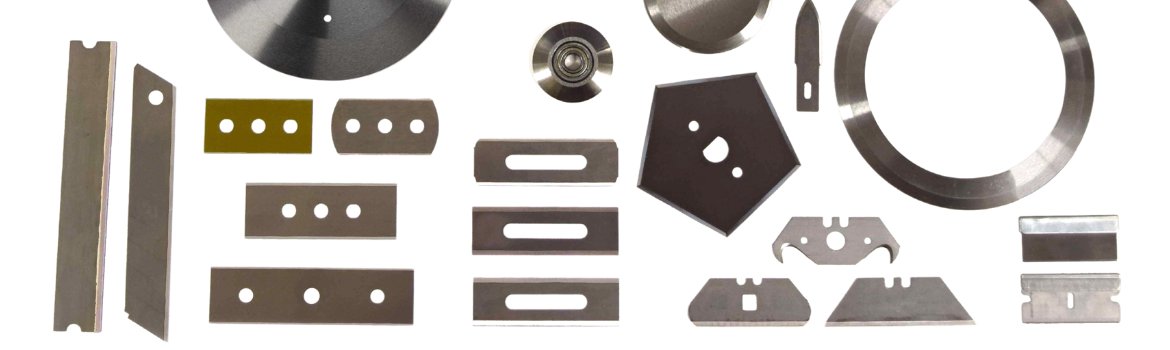
Maintaining a sharp blade is essential to optimized shear slitting processes. A sharp blade ensures the highest-quality cuts and lowest dust production. Precision-fit, sharp knives also enable optimum nip point setting to provide the longest blade life.
When shear slitting blades dull, the slitting operation stops while the entire bar is removed and the blades are replaced. Downtime for this type of maintenance can be several hours. Production losses are compounded when the blades dull in the middle of the roll resulting in scrapping the remainder of the material. Selecting an ideal blade material for the application and run-time requirements prevents costly downtime and material losses.
Expert knife manufacturers analyze the material to be cut, current blade selections, run-time requirements, and budgetary needs before recommending the best blade material for a specific shear slitting application. The right material provides a perfect mix of toughness, hardness, cost, and flexibility.
52100 Steel
52100 steel has the lowest wear life and as such, is rarely recommended for shear slitting applications. Shear slitting machines that employ 52100 steel blades must undergo frequent maintenance to replace dull blades. Knives manufactured from this material are low-cost and are not usually sharpened. Instead, the dull blades are discarded and replaced with new blades.
However, this blade material is required in shear slitting of specific plastic materials since it generates low amounts of heat during the cutting process.
D2 Steel
D2 steel is the most commonly used material for both top and bottom blades. It has a long wear life and is easy to sharpen. It is also a versatile material and can be used in shear slitting applications involving both plastics and paper. It is typically the most cost effective option for both wear and low budget applications.
M2 Steel
This steel is also commonly used for both top and bottom blades and provides increased wear life since it is harder and tougher than D2 steel. M2 is often recommended in shear slitting applications involving non-woven materials and paper since each is very abrasive and cause blades to wear quickly.
Switching from D2 to M2 allows operators to increase run-times between blade changes resulting in less maintenance-induced downtime.
CPM 10V
Prized for its wear resistance, this steel type is ideal for applications that demand long run times and varying materials (multi-layer plastics, papers, and non-woven materials). Blades crafted of CPM 10V steel are easily sharpened which helps to offset the higher costs associated with procuring blades from this material.
Carbide Inlay Blades
In environments that demand 24 x 7 run times, carbide inlay blades are an ideal choice for the bottom blade. Carbide maintains sharpness through slitting long rolls of abrasive materials. The inlaid blade is manufactured of D2 steel and carbide is inlaid only at the nip point to provide maximum benefit while minimizing cost.
Split Bottom Knives
Most shear slitting blades are a solid circular piece, making it impossible to change a single blade on a bar without removing every blade. As a result, every blade is replaced when a single blade dulls, chips, or breaks. Changing out every blade on a bar can take as long as four hours.
Split bottom knives allow operators to replace a single blade without removing all of the blades on the bar. Instead of a solid circular blade, a split bottom knife splits into two pieces allowing it to be pulled off and re-installed anywhere on the bar with only the use of an allen wrench.
When manufactured with a double cutting edge, a dulled split bottom knife can be removed and flipped to provide a fresh cutting surface in a fraction of the time required to change solid, circular shear slitting blades.
Selecting the right blade material for your shear slitting application is critical to maximizing up time and decreasing material losses and maintenance costs. Expert industrial knife manufacturers analyze your specific budgetary, material, and runtime needs to recommend an ideal shear slitting blade material and configuration.