Optimizing Your Granulator Blade Material
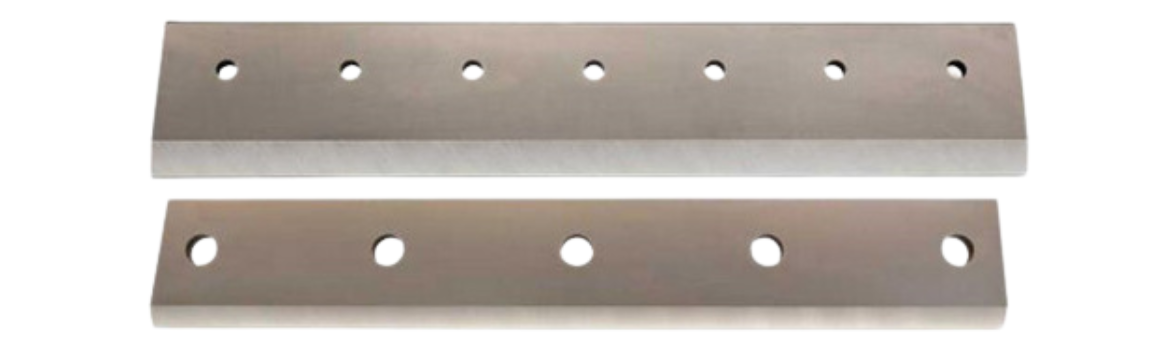
The cutting chamber of a granulator is where the most critical processes occur. It also contains the most essential replacement parts on your granulator, your knives. When the cutting edge of a granulator knife fails, the machine must use more energy cut. A failed knife edge also increases dust and fines, leads to poor regrind quality, and prevents the ability to produce uniform particle-size.
By concentrating on precision, one arrives at technique, but by concentrating on technique, one does not arrive at precision. “ Bruno Walter
A Balance of Toughness and Wear Resistance
The most common reason for premature granulator blade failure is improper blade selection. D2 steel hardened up to 59HRC Rockwell is commonly used to manufacture these knives and is appropriate for many applications. However, since every granulating operation is unique, it is imperative that processors evaluate their blade hardness to optimize knife life and output.
As steel is hardened, the material loses toughness, but gains wear resistance; in other words, it becomes more brittle but will last longer if used in the right environment. Finding the right balance of hardness and wear resistance is the first step in optimizing your blade material.
Producers of film trim each roll. The trimmed film is fed into a granulator for processing. The material to be granulated is consistent and contaminant-free, and there is no possibility of anything other than virgin film entering the granulator. In this environment, the best blade material has a high hardness level to maximize knife life. The toughness of the blade is not critical because the material to be cut is thin and consistent and free of possible tramp material.
In contrast, recyclers and plastic molders granulate a wide variety of materials. Recyclers of plastic water bottles may also find labels, screws, bottle caps, and staples within the material. This tramp material can cause the edge to chip leading to edge failure when the blade hardness is too high.
Plastic molders process a wide range of items, from thin, easy to cut plastics to dense, thick, hard, filled plastics. With such a wide range of items, many plastics molders find it necessary to use knives with lower hardness to accommodate all material types and prevent chipping of the cutting edge and increase blade life.
To evaluate the performance of your granulator blades, examine your blades after processing a normal run. Look for evidence of fraying edges or a sawtooth pattern on the cutting edge. If the edge is jagged or chipping, the hardness of the blade material is too high.
In addition to examining the edge of the blade, log the amount of material that is processed in-between blade changes. For example, your granulator may commonly process 100,000 pounds of material between blade changes. If the processing amount suddenly drops to 80,00 pounds, the granulator blades are wearing too quickly. If you find that your blades are dulling quickly, the knife hardness is too low.
Accuracy builds credibility. “ Jim Rohn
Customizing Your Granulator Blade Material
In many cases, granulator blade materials are too hard for the application, resulting in blade edge failures. It is common for knife manufacturers to harden all granulator blade steel to a standard condition that works well for 80% of applications. However, for the other 20% of users, the material is either too hard or too soft.
A high-quality knife manufacturer can provide customized hardness levels. For example, a blade of D2 steel can be hardened to 56 to 58 Rockwell. However, if there is a lot of tramp material present, it may be more beneficial to increase impact toughness by lowering the hardness a few points below currently used hardness levels.
In addition to customizing the hardness level, it may be necessary to evaluate the base material of the blade. While D2 steel is the most common, some granulating applications would benefit from a non-standard granulator blade material. When cutting dense materials modified A8 steel, which is commonly used for wood chipping blades, may perform best. Modified A8 steel has higher toughness than D2 steel at hardness levels between 56-58HRC.
Highly filled materials, such as fiberglass, ABS material, or rubber that are processed in environments with zero tramp material and can utilize higher alloy steels to increase knife life. Higher alloy steels have a higher wear resistance level. However, since granulator blades manufactured of this material are more costly, it is crucial to have the blades sharpened at the correct intervals to maximize life.
Other unconventional granulator blade materials, such as Lescowear steel, which is cold-work steel that can be hardened to 60 to 62 Rockwell but maintains the same impact toughness as D2 steel, provides increased wear resistance without increasing brittleness. In applications where higher alloy steels may be used, powered metal or carbide.
Optimum granulator blade material is a balance of toughness and wear resistance. To find the best mix for your granulating application work with a high-quality industrial knife manufacturer who can customize blade materials to meet your unique needs.