Advantages of Tungsten Carbide and Zirconia Ceramic Blades in Razor Slitting
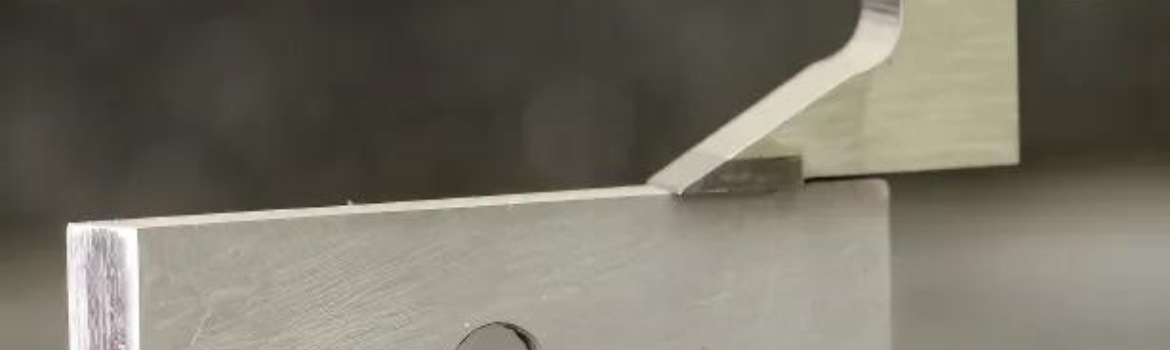
Razor slitting is a versatile cutting method commonly used for creating slit widths of light gauge films, tapes, ribbons, plastics, and non-woven materials. Choosing the right blade material for your razor slitting application ensures that you achieve maximize runtime and blade life while creating ideal cuts.
While many razor slitting operations employ steel blades, there are distinct advantages to upgrading to a tungsten carbide or zirconia ceramic blade.
Dramatically Increase Wear Life
Both tungsten carbide and zirconia ceramic blades provide significantly improved wear life over carbon steel blades. In fact, operators switching from carbon steel to tungsten carbide or zirconia ceramic can expect wear life to increase by 50 to 500 times.
Slitting operations halt during blade changes, decreasing overall production. Razor slitting blades are extremely sharp and require precise installation to enable maximum wear life and highest-quality cuts. Every blade replacement is an opportunity for operator-induced error and injury. While the material being cut, cutting speed, and angle all influence wear life, the cost savings over long material runs as a result of improved wear life is substantial.
Create Precise Cuts
In addition to a long wear life, the high hardness levels of tungsten carbide and zirconia ceramic hold rigidity in the application to create precise, pristine cuts.
Both tungsten carbide and zirconia ceramic are powdered metals that have very similar properties. Each time the blade is sharpened the binders in the material are stressed. Blades crafted from these materials can be sharpened up to three times. However, after three sharpenings, the lifetime of the blade is decreased beyond the cost savings associated with sharpening.
Extremely High Hardness, Zero Flexibility
The high hardness levels of tungsten carbide and zirconia ceramic that provide long wear life and precision cuts also make the blade extremely fragile. Mishandling can cause the blades to chip, shatter, or crack. If a cracked blade is installed into the machine, the blade will shatter as soon as it makes contact with the material to be cut. In fact, any impact from a side load (apart from the material to be cut) can cause the blade to shatter.
Switching from Carbon Steel to Tungsten Carbide or Zirconia Ceramic Blades
When switching from carbon steel to ceramic blades, the most critical investment will be in training operators on the differences between the new blades and the old blades. In many cases, carbon steel blades used in razor slitting applications are not sharpened. However, both of these blades are more costly than carbon steel blades so plant supervisors often elect to have these blades sharpened to extend their life.
Operators must also be trained on the handling of these extremely sharp and extremely fragile blades. When tightening the set screw against a carbon steel blade, operators can apply significant torque without damaging the blade. However, if the set screw is over-tightened against a tungsten carbide or zirconia ceramic blade, the blade will crack and then shatter when the machine is started.
It is also important to note that neither tungsten carbide nor zirconia ceramic blades are magnetic, which means that magnetic knife holders cannot be used.
Do You Need Make the Switch?
Both of these blades can be used in a wide variety of razor slitting applications, including plastics, paper-backed labels, tapes, and paper. However, since zirconia ceramic generates less heat during the cutting process than tungsten carbide, zirconia ceramic blades are recommended for some plastics applications.
Tungsten carbide and zirconia ceramic blades provide better cut quality, more efficient runs, and longer wear life than carbon steel blades. Incorporating these high-quality blades into your razor slitting operation can dramatically increase production while decreasing downtime and improving quality.