Services Offered by Top Slitter Knife Manufacturers
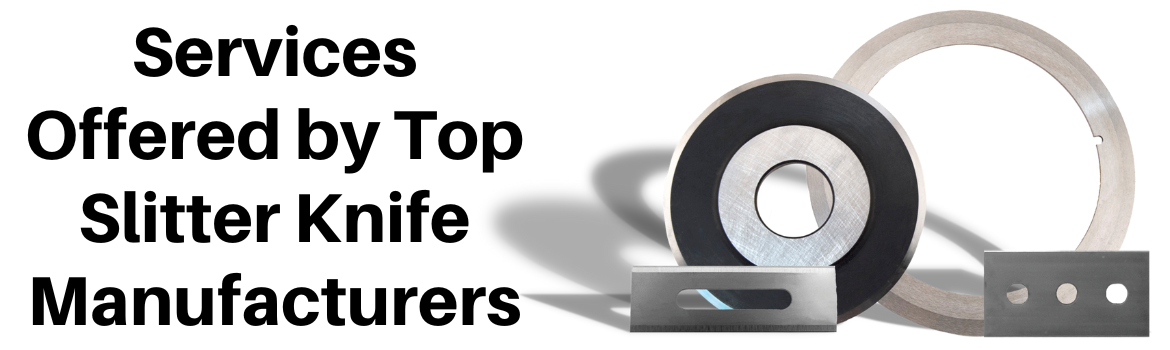
Maintaining high-quality, slitter knives improves both the production output and quality of your slitting processes. When selecting a slitter knife manufacturer, look for one with the experience to evaluate your entire slitting process operation, make recommendations to improve blade lifetime and cut quality, and supply you with slitting knives that meet the unique needs of your business.
Slitter Blade Sharpening
Sharpening your slitter blades allows you to extend the life of your current blades and decrease knife replacement costs. When sharpened by a professional, precision sharpening knife manufacturer, slitting blades are returned to like-new condition at a fraction of the cost of purchasing new knives. All that is required to sharpen slitting blades is to establish a relationship with a precision sharpener, collect the blades, and ship them out for sharpening.
To ensure maximum utilization of your slitting knives, establish slitter knife maintenance processes and procedures within your organization. For those with a consistent flow of slitting operations, a maintenance schedule founded on operation time may be the easiest and most effective to implement. To determine optimal maintenance frequency, collect data on slitting volume, material, and knife condition for a set period. Then create a schedule that ensures slitting blade condition is routinely assessed and that blades are sent for sharpening.
Creating a maintenance schedule ensures that you always have the best possible performance from your slitting knives. It also provides you with the data you need to maintain an adequate inventory of production-ready slitting knives.
Shear male and female knives, core cutting blades, scoring knives, , tungsten carbide, and zirconium ceramic blades can all be sharpened to maintain optimum slitting performance while decreasing replacement knife costs. Some blades can be ground as many as two to three times, which translates into significant savings. For example, sharpening carbide razor blades is often half the cost of purchasing replacement blades.
Some slitting configurations require knives to be sharpened as a matched set to maintain the balance and efficiency of the slitting operation. Additionally, machines may require minimum outer diameter grinds to ensure fit within the machine. High-quality, experienced slitter knife manufacturers, guarantee that your knives are sharpened to the precise tolerances of your slitting machine without removing excess material.
Preventive Maintenance: Don't start today by doing what you should have done yesterday. ~ Deniece Schofield
Knife Holder Repairs and Rebuilds
Shear knife holders require proper maintenance to ensure high-quality cuts and to optimize the life of shear slitting blades. Industrial knife suppliers with knife holder repair and rebuild capabilities test, inspect, repair, rebuild, and certify shear slitting knife holders. This ensures the best performance from your shear slitting machine and blades without requiring you to source a separate vendor for knife holder maintenance, repairs, and rebuilds. Utilizing your slitter knife supplier also eliminates the need to maintain these capabilities in-house.
To determine if your knife holder requires maintenance, work with an industrial knife supplier to troubleshoot your machine. When a knife holder needs maintenance, the most common symptom presented is poor quality cuts. Since poor cuts can be a caused by inadequate blades, not running at the right line speed, or problems with the knife holder, troubleshooting with an expert in both industrial knives and knife holders ensures identification of the true root cause.
Quality is never an accident. It is the result of intelligent effort. ~ John Ruskin
Wide Inventory of Custom and Stock Solutions
The wide variety of stock knife sourcing options makes it imperative to understand material certification processes, inspection criteria, and best-fit products. High-quality industrial knife suppliers offer only blades that are crafted from certified materials to meet exacting standards of quality, performance, and durability.
Industrial cutting applications require materials that adhere to the strict tolerances of slitting and converting machinery to guarantee optimal life, production, and safety. When your cutting needs change as a result of new materials, changes in production requirements, or new machinery, an experienced blade supplier discusses your unique needs and makes recommendations that best fit your business goals.
In some cases, this means employing a customized solution. For example, converters that utilize a bottom knife with a single cutting edge on a shear setup can significantly decrease maintenance-driven downtime by switching to a split knife bottom with a double cutting edge. This upgrade enables blade changes without requiring the removal of every blade from the shaft.
Industrial knife suppliers with large stock and customized options provide converters with the ability to find the solution that best fits both production and budgetary needs.
Partner with a vendor that offers a wide variety of in-house solutions, including blade sharpening, knife holder maintenance and certification, and both customized and stock blade options. Doing so decreases reliance on multiple vendors and provides simplified, one-stop access to expert consultants, recommendations, services, and products.