Should You Be Using Nikro Knives in Your Underwater Pelletizing Operation?
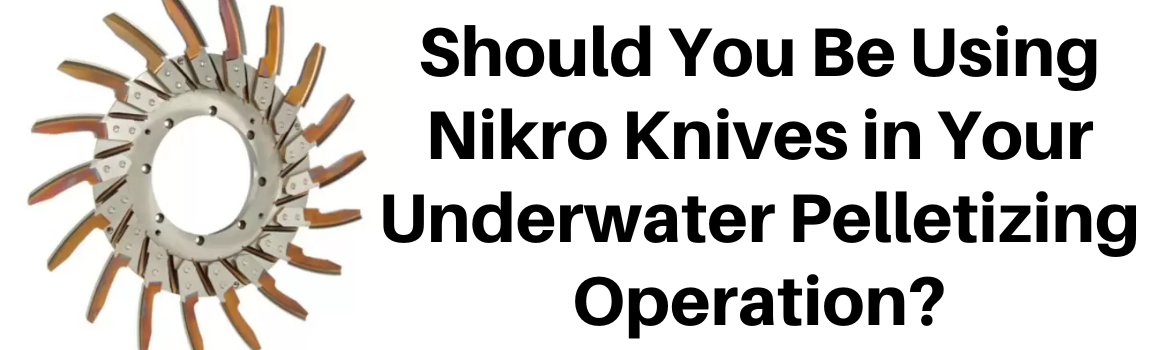
The balance of maintenance cost versus downtime is the most common question we receive from our industrial cutting customers. Maintenance-induced downtime is costly in so many ways. Obviously, when a machine is down for maintenance it is not running production; however, production loss is not the only factor. There is also the cost associated with replacement parts, labor, and maintenance materials.
Evaluating each factor that contributes to maintenance-induced downtime costs allows your business to make optimal decisions. For underwater pelletizing applications that demand maximum up-time, Titanium Carbide (TiC) blades may be an ideal choice. Blades manufactured of Nikro 128 or Nikro 143 provide substantially higher wear and corrosion resistance over standard tool steel and even tungsten carbide blades. As a result, underwater pelletizers can run 5 to 25 times longer between blade changes without impacting the productivity of the machine or pellet consistency.
Design is¦above all an effort to improve reality. “ Gianfranco Frattini
When is a Nikro Blade an Ideal Choice?
Pelletizing operations in which polymers are extruded through a die and then cut into pellets in a water bath, require knives that will maintain an edge underwater. Both Nikro 128 and Nikro 143 contain high levels of Chromium to increase corrosion resistance and Cobalt to increase hardness, thereby improving wear resistance. Nikro 128 is best suited to processing abrasive plastics. Nikro 143 is recommended for heavy wear and bending applications at elevated temperatures. Since Nikro 128 contains a higher concentration of chromium, it is often used in applications that demand increased rust prevention.
Failure is the opportunity to begin again, more intelligently. “ Henry Ford
What To Know Before Switching to Nikro Knives
Before switching your underwater pelletizing operation to Nikro blades, there are some considerations. First, Nikro blades are not ideal when running in contaminated environments. Any metals present in the water may cause significant damage to the blades and result in premature blade failure.
Since Nikro blades are extremely hard, they are also very fragile and will break or even shatter if mishandled or placed in contact with foreign material in the pelletizing process. In underwater pelletizing operations that frequently encounter metal inclusions, a high speed steel, such as M2, is a better choice. Additionally, in extremely corrosive environments, such as when cutting pellets that contain hydrochloric acid, Nikro may not be ideal. In these conditions, pelletizing blades do not wear, but instead slowly disintegrate.
Achieving Maximum Life and Minimum Maintenance in Underwater Pelletizing
However, in 90 percent of underwater pelletizing processes, Nikro blades provide an ideal combination of strength and hardness that substantially reduces maintenance-induced downtime. Initial setup costs when switching to Nikro blades include the cost of purchasing the new knives, and a Nikro or Carbide die face. Since pelletizing blades must wear before the die, replacing the die face with a material that is at least as hard as the new Nikro blade is essential.
Almost all quality improvement comes via simplification¦ of manufacturing, layout processes, and procedures. “ Tom Peters
Both Nikro 128 and Nikro 143 are more expensive materials than standard tool steels; consequently, blades manufactured from this material are more expensive. Operators realize a return on investment as they achieve longer runtimes with less maintenance-induced downtime. Not only do underwater pelletizers increase production, but labor dollars are maximized, and blade replacement frequency decreases.
Customers that utilize Nikro blades in their underwater pelletizing applications are investing in the future of their operations and focusing on the long-term gains that come from implementing the highest-quality materials. To determine if a Nikro blade is ideal for your process, contact an underwater pelletizing knife expert.