Understanding Pelletizing Materials
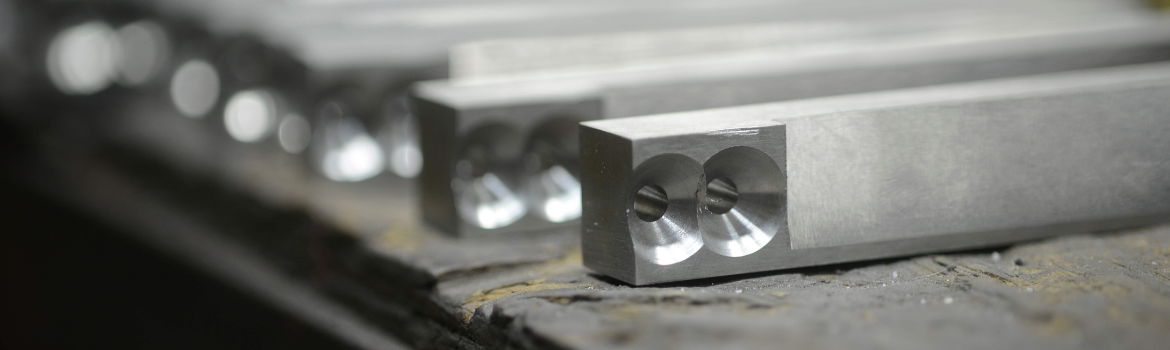
The pelletizing industry is so vast that addressing each possible pelletizer material is nearly impossible. However, most pelletizers fall into a handful of broad categories. Each of these groups has unique pelletizer blade concerns and requirements.
Two Common Types of Pelletizing
Pelletizing falls into one of two types: underwater and strand.
Underwater Pelletizers
Underwater pelletizers require blades that can stand-up to the harsh environments created during the pelletizing process. If the material to be cut is corrosive or acidic, a blade material that is tough, corrosion resistant, and possibly even coated with a wear resistant material may provide the greatest value.
Underwater pelletizing is often used to process recycled materials, which can be particularly abrasive to the pelletizer blade. Optimizing the blade material and geometry increases the life of pelletizer blades and decreases machine downtime.
Strand Pelletizers
Like underwater pelletizers, strand pelletizers commonly process polymers such as polyethylene, polypropylene, polystyrene, and abrasive material like titanium dioxide (Ti02). However, instead of processing recycled materials, which can often contain foreign materials and composites, strand pelletizers more commonly process virgin pellets.
A satisfied customer is the best business strategy of all. “ Michael LeBoeuf
Understanding Additives
For all pelletizers other than those processing virgin materials, additives are a constant factor in blade selection. The additive type determines how the material is pelletized and the best blade material. While the most common additives are talc, mica, fiberglass fill, and dye, toll compounders often work with many different types in response to customer demands.
By starting with virgin pellet, toll compounders melt, extrude, and compound the material before creating a pellet that meets exacting customer requirements. In many cases, additives are used to increase the toughness of the material. However, dye can also be mixed into the material to create pellets of a specific color.
The precision demanded by toll compounder customers often results in these pelletizers changing blades between every batch, even before the edge has dulled. The final product must adhere to strict requirements for color, shape, size, and weight and while the pelletizing blade may look clean, many toll compounders prefer to start each batch with a fresh blade rather than risk contamination and possible batch rejection.
There is only one boss in the company, the customer. “ Sam Walton
Finding Your Ideal Pelletizing Blade
For small batch processors, the right blade provides an optimum mix of cutting ability and value. With frequent blade change-outs, it is important that the blade choice be cost effective.
For large batch processors, such as producers of virgin pellets, the right blade is the blade that delivers the longest life. While these blades may come at a higher cost, the long-term value of decreased maintenance-induced downtime quickly offsets the cost and ensures highest possible output.
While large-scale pelletizers commonly employ a team of blade engineers, many medium and small pelletizers do not. At American Cutting Edge, we have a team of pelletizing blade experts that understand the unique demands of your industry and are prepared to evaluate your operation and find the best fit blade for your needs.