Meet the Face of ACE: Industrial Knife Sharpening with Chad Curry
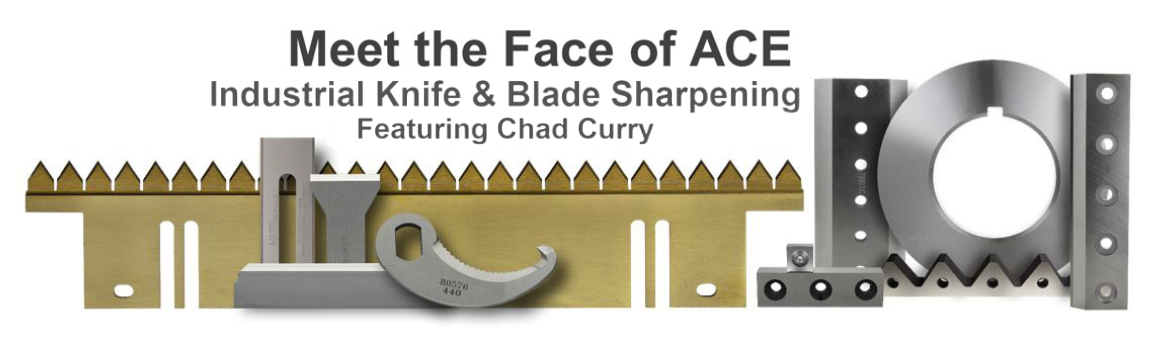
Overlooking the condition and care of your knives during route machine maintenance can be costly and dangerous. Knife sharpening and replacement is sometimes passed over instead of more critical maintenance needs. In some cases, the task of sharpening and maintaining knives is entrusted to a general machine shop out of convenience and expense.
Not all grinding and sharpening operations are created equally. When you work with a general machine shop, they have grinding equipment on-hand that can work a piece of metal and they probably have sharpening capabilities that work well in many circumstances. When it comes to the type of precision equipment you run for your cutting operation and the capital investment you've made in your machinery, you want to make sure that you're working with a true knife expert that has cutting application experience.
While you may save some money initially, working with a general machine shop that doesn't understand industrial knives can cost you more than just the price of sharpening. The wrong shop can negatively impact your cutting operation, damage your knives and equipment, and cost more money than you save.
Professionals like those at American Cutting Edge who have cutting application experience will know what needs to be done to provide the best outcome based on your knife's raw material, coating, and what you're cutting with it. Sharpening and refurbishing work should be performed so well that the end product is matched to new knife tolerances.
According to Chad Curry, American Cutting Edge's sharpening expert, working with an industrial knife specialist when you need to assess and sharpen your blades. Industrial knife manufacturers have specific knowledge of metallurgy, abrasives, and cutting applications. This level of expertise provides them with the ability to choose the correct combination of wheels and segments for your material. Not only that, they will also know what needs to be done to give you the best possible outcome for bringing your knife as close as possible to new knife tolerances, shares Curry.
Special grinding segments and coolants are required to provide exceptional quality and avoid over-machining the knife. We recently acquired a new sharpening customer who had been using a general machine shop to maintain their knives. After several ruined sets of knives, they decided a change was in order and they were amazed at the difference in quality. Their knives bowed from being run on the wrong type of machinery, says Curry.
Curry continues, In addition to bowing, machining on the wrong type of equipment without the right type of coolant can cause microfractures. These tiny cracks and imperfections in the knife are invisible to the naked eye. When a knife has micro-fractures, resistance can be lost to the material, causing a large crack in the knife, which can run quickly and can lead to knives blowing up. This is a huge safety concern. Blown knives can cause serious injury to personnel, damage equipment, and take your cutting operation off track.
In addition to sharpening and maintaining your knives, industrial knife and cutting operation experts can help diagnose what could be holding your cutting operation back from being more productive and profitable. Professional knife manufacturers has grinding experts on site that thoroughly inspect every knife for cracks, nicks, signs of wear and tear and help diagnose problems that your team might overlook.
The frequency of knife sharpening varies greatly from cutting application to cutting application. It depends on how long you're using the knives, what you're cutting, what material your knives are made from, and the efficiency of your machine's operation. We've had customers who have been able to greatly improve their throughput and quality of their end product just by making a commitment to keep their blades sharpened and properly maintained. There are a lot of reasons that influence how hard a machine is working. One potential cause is the condition of the knives. It's something that be easily overlooked but is a consideration, says Curry.
With over 55-years of industrial knife manufacturing experience, ACE has seen knives in every condition imaginable. Our customers rely on our expertise to help identify problems based on the wear patterns, cracks, and other damage when we look over their knives before sharpening. If we're not confident that the knife can be returned to working condition and deliver safe, consistent quality, we'll let you know that it's time to replace the knife.
Knives that come into our facility all go through the same assessment process every single time, says Curry. A clean and stable surface is critical to make sure that you get the best sharpening possible out of the knife. Knives can be cleaned by vibratory processing, sandblasting, or hand polishing. Afterward, a thorough inspection is done to carefully check for cracks, nicks, and any other signs of wear and tear. At this point, if we find that the knife has too much damage and is no longer safe to be used, we let customers know that, he continues.
Once a knife passes inspection, we determine which equipment is the best option for restoring a wear-resistant edge that lasts longer. A lot of customers don't realize that using the right equipment to sharpen the edge is important and it varies from knife to knife. Just because a grinder is right for a wood chipper blade, doesn't mean it's the right piece of equipment for a granulator blade, concludes Curry.
See the difference professional machine knife maintenance can make in your operation by putting the industrial knife and blade sharpening experts at American Cutting Edge to work for your cutting operation and contact us today. Not only do we have the experience and equipment to properly refurbish your knives, but we also know how to help you solve operational challenges associated with your operation.