Automotive Laminated Glass Manufacturing
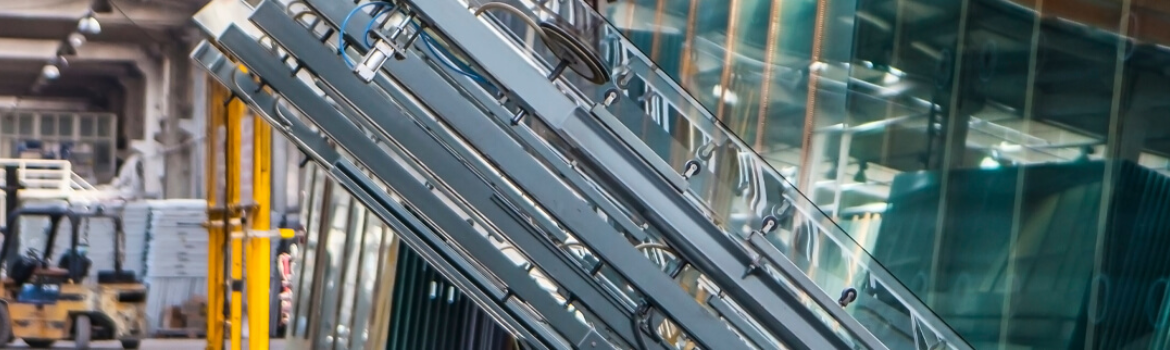
Most people don't associate industrial knives and blades with automotive glass. However, as with most products, industrial knives, and blades play an important role in manufacturing.
Automotive glass starts out as float glass and is transformed into what is known as laminated glass. Float glass is named after the manufacturing process used to create it. The raw materials literally float inside a chamber during part of the process. Since 1937, vehicle windshields have been required to be made from laminated glass for safety reasons.
Laminated glass, also known as sandwich glass, is made up of two pieces of float glass with a plastic layer in the middle that bonds to the glass. The middle layer of plastic makes the glass much stronger and shatter-resistant. If you've ever seen a broken car window or windshield, you probably noticed that the glass breaks almost into a spider web formation, keeping most of the glass from splintering into large sharp projectiles. The plastic layer that fuses between the glass is what keeps splintering from happening. Because laminated glass doesn't fall apart when broken, it is classified as safety glass.
Some of the more interesting properties of laminated glass include the fact that multiple layers of laminated glass can be used to create bullet-proof glass, most laminated glass naturally blocks up to 97% of ultra-violet radiation, and it is also a better sound insulator than other types of glass.
Making laminated glass is an intricate process that requires precision and accuracy along every step of the process including the seaming process and cutting excess material used for bonding both before and after the use of the infrared oven. Having a cutting edge that makes a clean cut and averages one blade per piece of glass is ideal.
- The laminating process begins with raw float glass.
- The raw glass moves to the cutting table where it is scored to be cut into smaller pieces.
- The scored glass goes to the break-out area where it is bumped and separated into individual pieces.
- The edges of the float glass are ground with an edge seamer to enhance the safety and durability of the edges. Edge seamers use an abrasive belt that rounds the edges of the glass.
- After the seaming process, the glass moves to the wash cycle to clean up any small particles to keep debris out of the layers in the next steps.
- The dust-free, temperature-controlled clean room is the next step of the process.
- In the cleanroom, an interlayer of plastic (PVB) or resin is placed on top of a piece of float glass.
- Another glass pane is put on top of the interlayer and any excess interlayer is cut
away using a blade (Recommended ACE item numbers (H-020003, SE-015004, SE-015004RC-U, SE-015011, SL-022501)
- The adhesion process begins with the glass sandwich moving through an infrared oven, which bonds the glass panes to the interlayer.
- The panes are moved into an autoclave, which is a pressure vessel that uses steam under pressure to remove moisture and finalize the interlayer's adhesion to the glass. The panes are heated to an appropriate sterilization temperature for a specific period.
- Once removed from the autoclave, the laminated glass is given a final trim to
remove any excess interlayer (Recommended ACE item numbers SE-015004, SE-015004RC-U, SE-015011, SL-022501, T-024001).
- The final step is to inspect the panes to be sure they are free of defects.
Working with a supplier that acts as a partner can have a ripple of positive effects on the production line. ACE customers experience improvements in everything from higher quality and fewer rejected panes to improved production planning via the implementation of warehouse agreements to manage the supply and demand of the items your organization needs.
Reach out to the cutting application experts at American Cutting Edge to learn how our expertise can translate into more efficient cutting applications.